How HBS Tracked and Installed 53,696 Medical Equipment Products for the Penn Pavilion Project
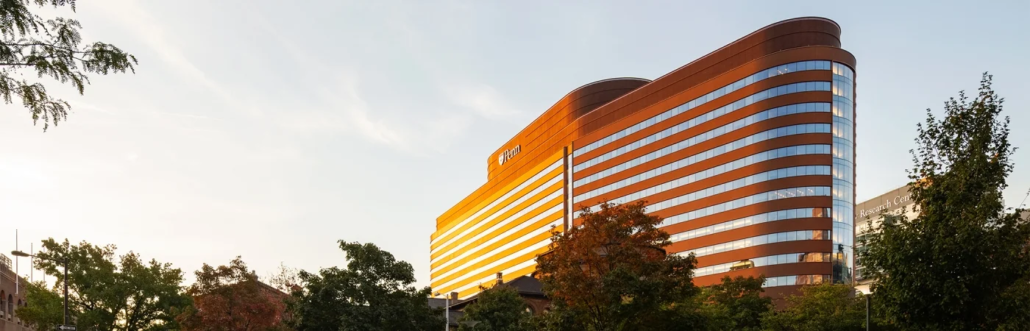
Project Background
Marking a historic milestone for Philadelphia and beyond, Penn Medicine recently opened the doors of its 1.5 million-square-foot future-ready Pavilion.
The $1.6 billion healthcare facility — the culmination of years of planning and construction — represents the latest piece of Penn Medicine’s connected medical campus, which includes The Hospital of the University of Pennsylvania, the Perelman Center for Advanced Medicine for Outpatient Care, and the Smilow Center for Translational Research. It is the largest capital project in the University of Pennsylvania’s history, the largest hospital project to be constructed in the Philadelphia region, and one of the largest projects in the United States.
Penn Medicine selected HBS to complete the medical equipment planning and to provide transition planning, facility activation, and regulatory compliance services for the 17-story, 504-bed hospital that also includes 47 operating rooms and a 61-room, two-story emergency department.
Founded in 2006 with offices across the US, HBS offers a synergistic suite of services that facilitates the planning, design, delivery, transition, and activation of new projects and ensures regulatory, operational, and safety compliance in existing facilities. As former hospital administrators, facility managers, clinicians, and Joint Commission regulators, HBS partners with clients to solve problems, remove inefficiencies, improve operational outcomes, and reduce costs so they can focus on their core mission.
The Challenge
With over 53,696 medical equipment products to track and install, HBS recognized the team needed to produce timely and accurate reports that kept multiple stakeholder groups up to date on the project’s status.
Jay Hornung, ACHE, CHFM, President, and CEO of HBS, sought out a solution to augment their in-house tracking system and was intrigued when he was introduced to FreightTrain’s innovative cloud-based solution, FitUp.
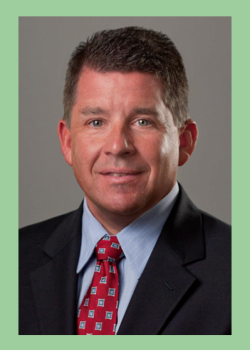
”The Penn Pavilion project was HBS’s first experience with FitUp. The result was so positive for our team and the client that we see FitUp as an essential tool for delivering the quality of service on which HBS has built its reputation.”
Jay Hornung, President, and CEO of HBS
The Solution
FitUp eliminates the need for antiquated spreadsheets and manual updating through a cloud-based system that allows leadership, project teams, and contractors to view the project’s status visually, in real-time.
Utilizing FitUp, HBS team could easily track the status of products and anticipate potential bottlenecks through their project dashboard. In addition, the FitUp software produced individual Room Cards that could be easily printed and hung on room doors that identified exactly what equipment needed to be installed in each room, including specific details regarding the vendor, manufacturer, model, quantity and if the product was new or leased on a room-by-room basis. The software can also be customized to included user specific Clinical Engineering tagging information, contributing significantly to a streamlined installation process.
It is not unusual for products to be damaged in transit or storage and need to be repaired or replaced. Typically, these issues are addressed by sending emails or making phone calls to track down the right person to resolve the case, then constantly following up to see that the problem is resolved. FitUp enabled the HBS team to automate the issue management process and track the status through a single interface, with all issues and status in a single location.
FitUp’s automated reports enabled the team to eliminate the painstaking process of preparing weekly reports, saving time and providing a high-quality tool for senior management to stay abreast of the project’s status.
Additionally, HBS was able to use FitUp to track purchase orders, receiving and room-readiness documents, and all the other documents needed to reconcile invoices.
”FitUp saved us time by creating reports to show our clients the status of the building load-in. We were able to quickly find the status of products with FitUp and relay any potential issues that could arise. Issues were tracked and fixed promptly with updates from responsible parties via FitUp.”
Luis Bonilla, HBS Project Director
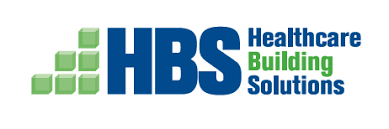
The Results
HBS credits FitUp as one of the primary reasons they were able to open the hospital on time after significant delays due to COVID construction shutdowns. FitUp assisted the HBS team by making the activation process efficient and helping keep their client’s senior leadership aware of the project’s status every step of the way. Crucially, FitUp gave the HBS team accurate, real-time data across the project variables, so the HBS team was able to respond quickly and with confidence to issues that arose during the project.
– Faster issues resolution
HBS processed 6,678 issues over the course of the construction project. Prior to implementing FitUp, it would take HBS more than 10 minutes per issue to create a report for the issue and then email it to someone who could resolve it. FitUp reduced that time to less than 2 minutes per issue, saving HBS over 1,000 man-hours on issues tracking alone.
– Faster, accurate invoice reconciliation
FitUp enabled the HBS team to have Purchase Orders, receiving reports, and packing slips in one easily accessible location. This documentation and the capability to have product delivery and installation verified in FitUp allowed HBS to quickly reconcile invoices and allow the client to pay invoices on a timely basis.
– Seamless project management
Before FitUp, HBS had to walk with drawings or a list to confirm what should be in each room. With FitUp’s Room Card door reports, they can see everything that should be in the room along with the layout drawings from a tablet.
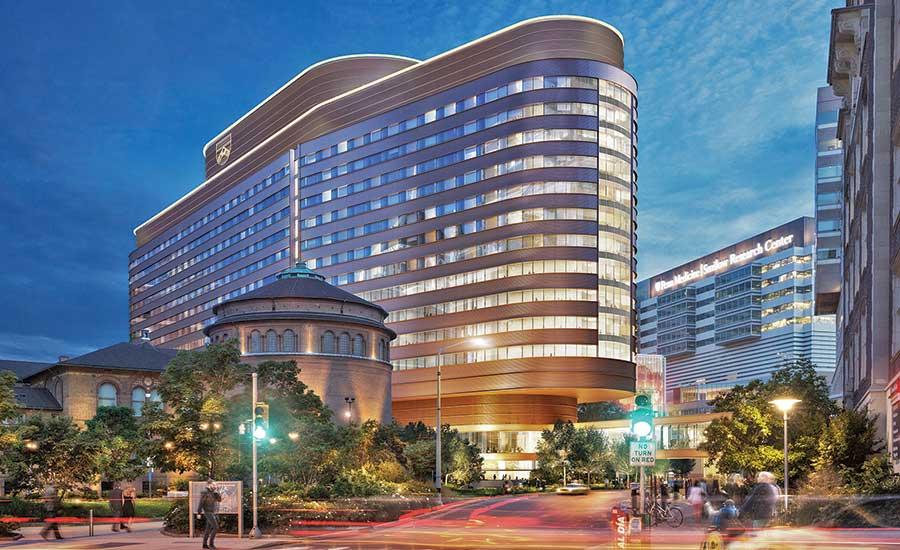
Leave a Reply
Want to join the discussion?Feel free to contribute!